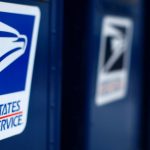
Behind the scenes at the FedEx nerve centre
At 1.30am on Wednesday, managers at FedEx's main US package handling facility at Memphis airport faced a difficult decision in the middle of their busiest week of the year. Parcel sorting was supposed to finish for the night at 2.07am, leaving enough time to get items to their final destination anywhere in North America before lunchtime. But two inbound FedEx aircraft from California were running late, meaning their cargoes risked being stranded in Tennessee.
"We have to weigh up the cost of leaving those packages behind against the cost of holding up the whole operation to wait for them," said Marla Waldheim, a systems administrator. "If the outbound aircraft are held back too long, some might miss their landing slots and then the delays start rippling through the system."
As the lights of the late aircraft twinkled into view shortly before 2am, a decision was taken to extend the deadline by 20 minutes – enough time to unload and redirect the delayed cargo. By 2.30am, outbound aircraft packed with parcels were screaming down the runway destined for points all around the world. For the next two hours, Memphis was the busiest airport on the planet, with FedEx jets taking off at a rate of one every 50 seconds.
Mini dramas such as Wednesday night's are not unusual in the weeks running up to Christmas, when FedEx handles 40 per cent more parcels than usual. Monday was the company's busiest day of the year, with 8.1m packages having passed through its system, compared with the daily average of 5.5m. Everyone at FedEx understands that their collective performance over the festive season can make or break the company's year.
"We start planning for Christmas the day after (the previous) Christmas," says John Dunavant, FedEx's managing director of global operations control – the man responsible for keeping packages moving as smoothly as possible around the world.
Volume starts increasing as early as August or September as retailers and manufacturers prepare for the rush. International business peaks in November as Asian-manufactured consumer goods surge into North American and European retail outlets. Domestic markets are busiest in mid- December as gifts are exchanged among families and friends, and goods ordered through catalogues or the internet arrive on people's doorsteps.
"Ninety per cent of the package flow is predictable – but that other 10 per cent can really throw you," says David Rebholz, executive vice-president of FedEx's US operations and systems. "This year will be interesting because Christmas day is a Saturday, so people will keep on shopping late into next week. Parcels do not have reservations, so you just have to make an educated guess about demand."
Mr Dunavant monitors the movement of the company's 500 daily flights from his Memphis "war room". A giant screen on the wall shows the location of every FedEx aircraft in the sky, with dense clusters over North America and Europe and four winging their way across the Pacific from Asia.
Twice a day, Mr Dunavant conducts conference calls with 250 managers around the world to review the previous 24 hours and plan ahead. Spare aircraft and crews are located strategically around the world in case an aircraft breaks down or demand exceeds expectations. "We try to build as much redundancy into the system as possible while keeping the system efficient," he says.
The biggest threat to the operation is bad weather. A typhoon in the Philippines last month forced FedEx to close its Asian hub at Subic Bay and redirect flights to Taipei. In the US, FedEx has a second large hub at Indianapolis that could take over if Memphis was closed.
Next door to the "war room", a team of meteorologists scour satellite pictures for signs of any weather that could disrupt flights and the Weather Channel plays continuously on a television monitor.
On Wednesday morning, Memphis was at the centre of ahigh pressure system that gave clear skies and perfect flying conditions but brought bitterly cold temperatures for the 12,000-strong FedEx night shift.
About three-quarters of all FedEx packages sent to or from the US pass through the Memphis facility and its 300 miles of conveyor belts. Among the waves of packages flooding into the giant sorting houses on Wednesday morning, the most easily identifiable were countless boxes bearing the names Dell and Hewlett Packard, signalling strong sales of computer equipment.
Donald Colleran, FedEx's head of express freight sales, said i-Pods, the digital music players made by Apple, were another hot item this Christmas. Luxury goods, such as Louis Vuitton handbags and Gucci clothing, were also moving in large numbers.
The sorting process is almost entirely automated with infrared beams reading a barcode on each package to identify its destination and directing it to the correct aircraft. Details of packages arriving from overseas are provided to customs authorities in advance to avoid hold-ups. Items requested for inspection are automatically diverted to the on-site customs office. Robert Carter, FedEx's chief information officer, says this technology has allowed FedEx to tighten security in response to concern about terrorism without slowing down the system.
Chris Bickerstaff, a service assurance manager on the night shift, says there is still a human touch despite the high level of automation. "We are trained to treat every package as if it's the golden package," he says. "There are some cases you get drawn into, such as making sure someone's cancer treatment gets on the plane, or getting a child's dress to a christening or a pair of wedding rings to a ceremony in the Bahamas the next day."
Ms Waldheim recalls that just a decade ago the sorting process was done by hand, and it is only 31 years since FedEx was launched from an old second world war hangar on the Memphis site it occupies today. On its first night of service, the company delivered 186 packages. Now, the facility sprawls over 300 acres and handles hundreds of thousands of packages daily.
Fred Smith, the former marine who founded the company, remains its chairman and chief executive.
Many of the company's management team, including Ms Waldheim, Mr Dunavant and Mr Rebholz, have risen through the ranks after joining as package handlers or couriers. "There is a lot of purple blood running through people's veins here," says Ms Waldheim, referring to the company's corporate colour.
Another former package handler is Reginald Owens, now the man in charge of the Memphis hub. "You get a tremendous sense of satisfaction at the end of each night when you see the last aircraft up in the sky – because you know how much work has gone into getting it there."
SANTA'S REAL BOBSLEIGH: THE FEDEX STRATEGY
* The leader: Fred Smith, a former US marine, founded Federal Express in 1971 after spotting an unfulfilled demand for rapid delivery of small packages across long distances
* The challenge: to increase volume to as much as 8m packages a day during Christmas to destinations in 215 countries
* The customers: individuals sending gifts; companies delivering orders to consumers; retailers receiving goods from suppliers
* The resources: 600 aircraft, 70,000 vehicles, 104,000 employees and contractors
* The locations: American hubs in Memphis, Indianapolis and Anchorage; European hub at Paris Charles de Gaulle airport; Asian hub in Subic Bay, the Philippines
* The competition: UPS, DHL, TNT
* The risks: bad weather, mechanical breakdown, uncertain demand, labour shortages, terrorism
* The safeguards: airports ready to take over in case of hub closure; spare aircraft and crew on standby; employee bonuses offered for good performance and corporate staff encouraged to volunteer for hub operations; close co-operation with customs, the Federal Bureau of Investigation and Department of Homeland Security.