
The Challenge of the New: UK Mail welcomes Operations Director
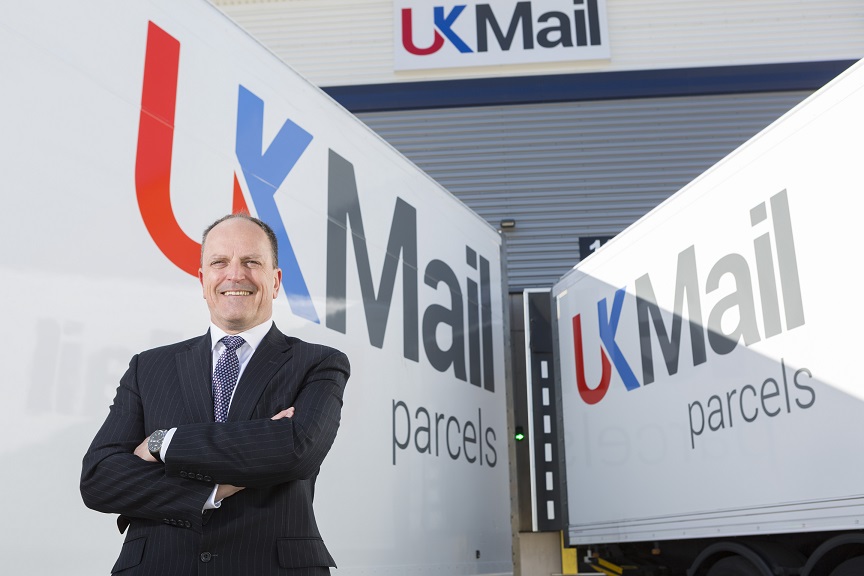
Peter Fuller, who joined UK Mail in April as Group Operations Director, talks to Post&Parcel about how he is settling into his new role – and how the company is working to get the full benefit of its automated hub in Ryton, Coventry, which started operations last year. As the former Operations Director of Parcelforce Worldwide – where he put in almost two decades of service – Fuller is certainly not a newcomer to the industry or the world of large companies. But, as he freely admits, UK Mail does present a rather different challenge.
“Parcels are important to us, but UK Mail is not just a parcel business,” says Fuller. “It is a more complex business and I am still learning about the range of operations – for both mail and parcels.”
There are, however, some important similarities between Fuller’s past and present roles.
“In both jobs,” Fuller explains, “I have managed large investments – bringing new depots and hubs online and making them work.”
“And that is my immediate first priority at UK Mail. We are focused on making the new automated hub work as efficiently as possible and, importantly, integrating its operation seamlessly with the other hubs and depots.”
UK Mail moved from its old Birmingham facility to Ryton in July last year and – as Fuller concedes – there were teething problems which clearly had an impact on the group’s operational performance and financial results.
But, speaking to Post&Parcel today, Fuller says that the company has addressed the issues and Ryton is now working well. Throughput is rising steadily and the hub recently processed its 30 millionth item.
One of the issues associated with automated parcel sorters is that they are not so good at handling out-sized items. However, the ability to handle these “non machinable” consignments is something that UK Mail regards as a “key differentiator” which sets it apart from competitors who are 100% automated.
So, in order to maximise the benefits of automation at Ryton and process the non-machinable consignments (which are an important and growing part of the business), UK Mail has recently added a cross-dock central hub which is used principally for these items.
Even though the hub is performing well, Fuller says that UK Mail will always be looking for improvements. Change is constant.
“Managing an advanced automated system is like running a sports car,” explains Fuller. “You can’t just turn the key, put the pedal to the metal and hammer it all day. You have to take care of it, service it, and fine-tune it to get the maximum performance.” And of course – stretching the analogy a bit – you have to keep innovating, by upgrading the equipment and keeping a close watch on tomorrow’s technologies.
Fuller tells us that UK Mail has also been in discussions with some innovative service providers. “I believe that we should always at least look at these ideas. It is worth taking some time out of the day job to keep track of new developments. Of course, some things offer more potential than others,” says Fuller. “If the right sort of investment opportunity comes along, we will consider it.”
The implementation of new equipment has to go hand-in-hand with staff training and development. Fuller tells us that the Ryton hub currently employs about 250 people – which is significantly more than the old facility – and there is a strong training programme enabling UK Mail to handle the expected growth in annual volumes and, of course, successfully manage the “peak seasons”.
A key element of “peak management”, of course, is making sure that sorting capacity is aligned with the customers’ forecasted volumes and – just as importantly – ensuring those forecasts are accurate. Fuller says that UK Mail has built up strong relationships with its clients so it can have confidence in both the forecasts and its ability to deliver; but – just to be on the safe side – he will not be wishing for a White Christmas or a snowy peak season!