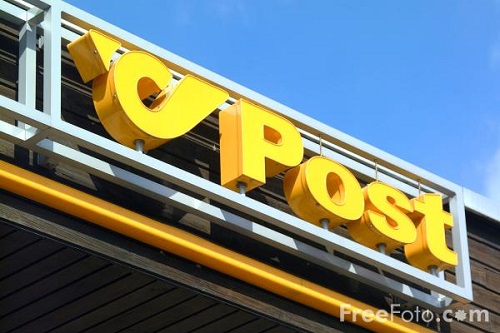
UPS system delivers savings; UPS has spent USD600 million to automate package sorting and cut time, miles and cost. For drivers, it's a real help.
When Rick Schetinski starts his United Parcel Service truck each morning, he no longer worries about overlooking packages during a rapid-fire delivery schedule averaging 17 stops per hour.
Thanks to a huge computer-automation project at the Maple Grove distribution center where his truck is loaded, Schetinski receives a list on his handheld computer of everything in his truck and where it's going. "In years past, the truck was loaded but you didn't know what was in it" or where it was, Schetinski said. "It would take you 20 minutes a couple of times a day to go through the truck to see what you had."
UPS says the automation system – akin to putting the Dewey Decimal System in a library to replace random book piles – is a key to handling increasing package volume, up 8 percent this year, and coping with the increased volume of holiday deliveries. The Maple Grove distribution center, one of three serving the Twin Cities, expects a peak volume of 86,000 packages a day around Dec. 20, up from 59,000 packages a day the rest of the year.
Automating a fleet of delivery trucks is quite a feat considering that the back of a United Parcel Service truck resembles a cardboard-box jungle. Hundreds of boxes and envelopes crowd the floor and eight shelves in each truck, differentiated only by small labels that spell out their destinations.
But bringing order to the jumble of packages is the aim of a USD600 million, six-year nationwide software project at Atlanta-based UPS. As a result, UPS has become a leader in using automation to improve the efficiency of package delivery, said Brian Clancy, an analyst with MergeGlobal, a freight and logistics consulting firm in Arlington, Va.
Because UPS depends on a single fleet of brown trucks to handle packages that were shipped by ground or air, "optimization of those trucks gives UPS more bang for the buck than it would for their competitors," which include FedEx, DHL and the U.S. Postal Service, Clancy said. FedEx, for example, uses different fleets for different types of cargo.
Right packages, right truck
Two years ago, the new software came to the UPS distribution center in Maple Grove, where Schetinski's delivery truck and 226 others are loaded every morning by a computerized system called Package Flow Technologies.
Packages are unloaded from cross-country semitrailer trucks, pass through a spider's web of conveyor belts and have their shipper-provided bar-code labels scanned for delivery information. UPS managers use the data to map out a next-day delivery plan for the trucks, and the software then generates new labels that give each box an "assigned seat" on a particular vehicle.
This list of what's aboard is sent wirelessly to a specialized personal digital assistant carried by each driver – the same device that people sign when a package is delivered. At the touch of a button, the driver can determine his or her next stop and the number of pieces to be delivered there.
"It usually works," said Schetinski, a UPS driver for 23 years. "You sometimes get a package that doesn't belong in your truck, but not often."
The package-flow software saves money in several ways, said Dean Thesing, a Twin Cities coordinator for what UPS calls its "Center of the Future." It streamlines loading and unloading delivery trucks so fewer workers are needed and less training is required; a team that used to load three trucks in four hours can now load four trucks. It also speeds up deliveries, so that a driver on average can make 16 extra stops per day, for a total of 136, he said.
In addition, the software has cut in half the number of delivery mistakes that force drivers to retrace their routes later in the day, Thesing said. That's because the software minimizes errors caused by packages being sent on the wrong truck or being lost beneath the jumble of boxes on the right truck. Previously it wasn't uncommon to go back two or three times to some stops, Schetinski said.
More packages, fewer miles
As a result, Maple Grove's trucks are driving the same or slightly fewer miles each day, though the number of packages delivered is up several percent this year, Thesing said.
Collectively, the hundreds of UPS trucks driven in Minnesota have cut an estimated 353,755 miles over the past two years.
The software also allows better route planning. That already is something of a science at UPS, which has sought to minimize the number of left turns a driver must make, wasting time waiting for oncoming traffic before turning.
Using the Package Flow Technologies software, Maple Grove dispatchers can adjust the next day's routes throughout the night, Thesing said. The facility is electronically notified of a package's destination the moment it is shipped, enabling dispatchers to forecast the ebb and flow of packages and adjust delivery routes accordingly, he said.
"Before, we planned the delivery-truck routes once a month and adjusted them every day," Thesing said. "Now we can forecast 94 percent of our arriving packages, so we plan the routes every day and finalize them at 3 a.m."
The software project began in Georgia in 2001 and three years later debuted in the Twin Cities, which is one of UPS' top 10 U.S. shipping points in terms of volume, Thesing said.
Older plants in Minneapolis and Eagan use Package Flow but aren't easily retrofitted with the maze of conveyor belts and automatic sorting and loading equipment found in Maple Grove. That four-year-old center is "as automatic a sorting facility as UPS has anywhere in the world," Thesing said.