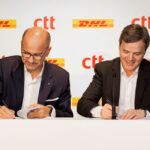
DHL provides Jaguar Land Rover solution
DHL Supply Chain has launched a pan-European, in-bound logistics solution for Jaguar Land Rover (JLR). A DHL statement said that the move would see a “considerable cost reduction and more responsive logistics planning. This follows the successful implementation of the UK parts collection service for the vehicle manufacturer in August 2008.”
”As lead logistics provider (LLP), DHL’s freight control tower has been a key success factor in the European element of the in-bound logistics function, involving 500 automotive component suppliers in 17 countries. Acting as LLP, DHL plays a central role in planning and managing other supply chain service providers on behalf of its customer.”
The JLR European in-bound collection service is one of the largest of its kind in the UK, with over 980 full and partial load collections every week to sites in Castle Bromwich, Solihull and Halewood. Within weeks of implementation, DHL has confirmed a measurable improvement in supply chain efficiency of over 10%, with further enhancements planned over the next few months.
”DHL has utilised its extensive knowledge of the European transport market to negotiate the most competitive carrier rates available for the provision of transport. The new collection strategy uses a combination of transport services – full truck loads, milk round collections and groupage – to improve efficiency and reduce costs. DHL’s freight control tower in Veghel, Holland, manages and procures the most appropriate carriers, leveraging synergies with other DHL contracts operated in Europe,” the company said.
Laurie Cogger, vice president, Lead Logistics Provider Automotive, DHL Supply Chain UK, said: “This has been a hugely complex project to implement in a very short timescale – just four weeks from project approval to implementation – but one that has paid great dividends already. Our implementation of the control tower ethos, where we act as a 4PL, brings best practice and supply chain innovations, and has worked really well. This has been a real partnership between us and the JLR team.”
As part of the in-bound solution, DHL’s team based at the JLR facility in Solihull has focused on a number of areas to bring about greater visibility and control throughout the supply chain. A container management team has reduced reverse logistics costs by improved management of the pallet and container processes.
A new vendor management quality system has been introduced by the DHL team to investigate and solve delivery issues across the supplier base. DHL’s supply chain management system has been integrated with the JLR system to provide greater transparency and supply chain visibility.