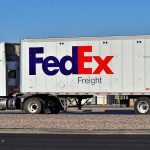
Integrating physical mail with the digital world : Lockheed Martin unit uses technology to channel information about mail to the right personnel.(Lockheed Martin system integrations distribution technologies business unit.)(Interview)
In the modern world, the easiest and most convenient way to send a message is via e-mail or through sophisticated data networks. Does that portend an end to physical mail, an event that has been predicted for two decades? Not quite.
Despite the quantum leap in technology during the past decade, corporations, universities and government agencies still send, receive and process millions of pieces of traditional, expedited and packaged mail annually. In many mailrooms, manual labor and considerable resources are utilized to process parcels.
Like Sherman's "March to the Sea," the flow of mail is relentless. It encompasses items ranging from letters to magazines to advertisements to parcels. Processing physical mail is critical to a company, and the management of such mail is typically separated from the information management systems that deliver, track and document other information assets throughout the enterprise.
Bridging the divide
But in today's technologically fast-paced world, integrating physical mail into the digital world is becoming increasingly important. A vital aspect of achieving significant productivity gains lies in a company's ability to seamlessly bridge electronic and physical processing technologies.
"There still is a world of physical mail, and we think there always will be," says Judy Marks, president of Lockheed Martin System Integration's Distribution Technologies business unit.
Marks, who was tabbed as president of the business unit in May, heads one of the world's leading organizations in design, production and integration of recognition, information, sortation and material handling equipment and systems. The company's biggest customer is the U.S. Postal Service (USPS). ADC technologies, including optical character recognition (OCR), have helped the USPS increase automatic machine read rates of millions of pieces of handwritten-addressed mail from 3% in 1996 to nearly 80% in 2000. It hopes to increase that figure to 93% by 2004. High-speed automation has helped the USPS save $50 for every 1,000 letters sorted. Those savings begin to add up when one considers the USPS handles billions of letters annually.
Building on past successes, Lockheed Martin Distribution Technologies has developed the Carton OCR product, which minimizes the time-consuming, labor-intensive task that a company spends on manually handling each carton that doesn't conform to its system. Through a partnership with Microsoft, Lockheed Martin is introducing ManageMail, a patent-pending solution that brings e-mail speed to physical mail management. The solution uses the data captured from mail handling and sorting systems by channeling information about the mail throughout the enterprise.
In an exclusive interview with Frontline Solutions, Marks explains how Lockheed Martin Distribution Technologies goes about providing that information to its customers.
Frontline Solutions: How important has it become to provide a solution that allows your customers to easily integrate new technologies into their existing systems?
Judy Marks: The issue of integration is near the top of every customer's priority list. Every customer has a unique legacy system that must be dealt with. The challenge for the customer is to sustain a business operation while migrating from the legacy system to a new IT platform that helps that company become more competitive in the electronic economy.
FS: Can you describe ManageMail, how it works and why it was developed?
JM: ManageMail is our first complete enterprise mail service management application. In the past, we served the physical mail needs and the electronic mail needs of our customers independently. ManageMail integrates the physical and information mail services. It bridges traditional mail services and sophisticated enterprise information systems to create a more intelligent and cost-effective mail service center.
By leveraging the existing information technology (IT) infrastructure, ManageMail enables faster, more accurate and less costly management of all traditional mail, including internal deliveries among individuals and departments. It automates the routing of incoming mail to thousands of employees. Those employees, as users, are also empowered to select priorities and delivery methods for outbound mail.
FS: What technology drives ManageMail?
JM: We adopted Active Directory, a solution included in Microsoft Windows 2000. The solution allows us to manage names and physical locations, and map electronic and physical addresses to each other on a real-time basis in a directory system.
We marry this information with our mail processing technology, which processes letters, magazines and inserts so employees can get the most up-to-date information on their mail, either physical or electronic, when they need it, where they need it. ManageMail provides a desktop portal that gives any employee using an Outlook Mail interface a full range of mail-related services and status information. Any user within any campus (a large co-location of people) has the ability through ManageMail to route information, whether it be electronic or physical.
FS: How do you integrate physical mail and other items with the digital world?
JM: We are applying recognition technology to multi-dimensional items, which in our world is a package or parcel. The challenge is to find a "region of interest" so the package can be identified. A package typically has six sides, so it's a physics challenge compared with a letter. As a package travels down the conveyor, or enters a distribution center (DC), or is outgoing on a pallet, you need to capture the attribute information within the region of interest on that package–be it a one- or two-dimensional bar code, an address field or other indicia.
All attributes eventually marry the physical piece of mail with information, allowing customers to effectively run their enterprises. Our Carton OCR product performs this function. The challenge, from a technology standpoint, is capturing multiple images for each package or carton in high-speed applications, identifying the region of interest, applying recognition algorithms, and returning the information required for customers to sort and parse their products in real time.
FS: What is the main point in providing solutions to your customers?
JM: I challenge my team with four points: experience, expertise, commitment and teamwork. We take our experience–we're one of the world's best complex heterogeneous systems integrators–and our understanding of how to integrate solutions and technologies to meet our customers' needs on time and within budget. We marry that with some of our advanced recognition technology.
There is a cyclical process involved. We understand our customers needs, develop a solution, install that solution, and then continue to understand their needs and wants to enhance those products and create new ones.
FS: What is the next advancement in ADC technologies that will improve the service that Lockheed Martin Distribution Technologies gives its customers?
JM: Automatic carton and parcel identification, applying biometrics to identification solutions and enhanced forms processing are focal points for us. We're advancing automatic carton sortation and routing processes by enhancing carton identification technology. Six-sided image capture and high, accurate read rates are extremely important to increase productivity and significantly reduce the number of cartons or parcels that must be processed manually.
With biometrics and enhanced forms processing developments, our goal is to marry attribute identification with the enterprise database. When you can monitor, measure and analyze data in real time, you can greatly improve the management of your operation and realize significant costs savings.
RELATED ARTICLE: FRONTLINER
Judy Marks
Title: President of the Distribution Technologies business unit of Lockheed Martin Systems Integration, Owego, NY
Responsibilities: Oversees the development of integrated sortation and material handling systems and equipment for national postal agencies, including the U.S. Postal Service and its counterparts in the United Kingdom and Australia; commercial mail firms; and retail order-fulfillment applications.
Years with Lockheed Martin: Five
Previous experience: Marks joined IBM Federal Systems in Owego as a systems engineer in 1984 and has risen through the ranks to her current position. Her management responsibilities continued through two acquisitions of the Owego operations in the 1990s: by Loral in 1994, and when Lockheed Martin acquired Loral in 1996.
Background: Holds a bachelor's degree in electrical engineering from Lehigh University (Pennsylvania) and currently serves on the Association of Postal Commerce Board of Directors.
Quotable: "There still is a world of physical mail, and we think there always will be. Our goal is to provide information anywhere any time. Sometimes it's physical, sometimes it's electronic, and sometimes it's a hybrid."
Page 11;Volume 2;Issue 10
THIS IS THE FULL TEXT: COPYRIGHT 2001 Advanstar Communications, Inc.
COPYRIGHT 2001 Gale Group
©2001 Information Access Company.