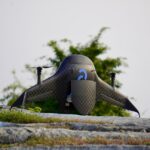
Pitney Bowes bounces back after major presort plant fire
Just 119 days after its largest US presort facility for First Class Mail burned to the ground, Pitney Bowes opened a brand new replacement plant in Grand Prairie, Texas, this week.
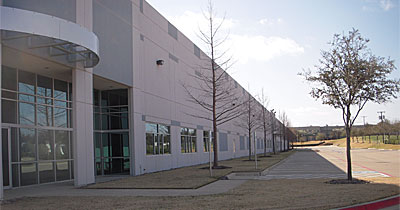
The new First Class Mail presort plant in Grand Prairie is close to the facility destroyed by fire last February
The new 161,000 square foot leased building is located at the Great Southwest Business Park, little more than a quarter of a mile from the facility destroyed exactly four months ago yesterday.
When it gets up to full speed within the next few months, the new facility is expected to presort more than 1.6bn pieces of First Class letter mail each year.
With 400 to 450 staff, the facility will have a similar capacity to the 400,000 square foot plant lost in the catastrophic fire just after Superbowl weekend back last February.
Installation of equipment is set to continue through to mid-July for the building to house 25 letter sorting machines and two flats sorting machines.
Speaking to Post&Parcel yesterday, Pitney Bowes’ president of mail services, Jay Oxton, spoke of his pride in the achievement of his team in getting the replacement plant up and running in such a short space of time, minimising distruption in the mean time and retaining almost all employees from the original facility.
“I’m very proud of what our local management team has been able to do – we’ve retained 98% of our employees from the date of the fire to yesterday,” he said.
Oxton also praised his team for redirecting the Grand Prairie mail volumes to nearby plants and working well to keep clients content.
He said: “We’ve retained virtually all of our clients, and my team has really kept in great communication with our customers, and we think we’re in a pretty good position to continue to grow our business in that market.”
Fire
The fire on started in a retail logistics warehouse next door to the Pitney Bowes facility on the night of February 7th, engulfing the presort plant at about 4am that night.
However, no official details have been released regarding a cause of the fire, which had completed destroyed the presort plant by 7am.
Praising the US Postal Service for a “great job” in supporting and adjusting to the significant changes in operations following the blaze, Oxton said all requested customer pickups were made within 24 hours of the fire.
Nine extra sorting machines were installed at other Pitney Bowes sites in the Dallas Fort Worth area by February 14th, and Grand Prairie staff relocated to those sites, so that normal services could resume.
Lessons learned
Oxton said that although his team had been “outstanding” in dealing with the disaster and its aftermath with alternative arrangements quickly adopted thanks to the company’s business continuity planning, he revealed candidly yesterday that some important lessons had been learned nevertheless.
In particular, he said that although there had been “confusing messages” at the time regarding the likely impact of the fire, initially local managers could have swung into action a little sooner to notify key clients and executive management about the situation.
– Jay Oxton, Pitney Bowes
In some cases, Oxton said, managers may have been waiting for approval for decisions, rather than knowing that in the case of disaster, they were authorised to move ahead with business continuity plans.
“We’ve learned quite a bit from the fire,” he said. “Making sure that our clients understand the ramifications of our business continuity plan is an area where we’re now going to spend a lot more time at an executive level, making sure clients understand here’s how we handle this process.”
Growing business
With the new plant now up and running, Oxton said Pitney Bowes could now focus on growing its business again in the area. Although First Class Mail is declining in the US, he said the automated, business side of First Class Mail was not declining as much as First Class as a whole.
The nationwide, diversified nature of Pitney Bowes’ portfolio of presort clients also protects it from declining volumes, he suggested, meaning that while businesses in America are consolidating their mail production facilities to cut costs, his company can pick up extra business.
He said: “The fact that we’re one of the only nationwide presort service providers, that puts us generally in a pretty good position.”
Across the US, Pitney Bowes now has 36 facilities processing 14bn pieces of First Class and Standard Mail each year.