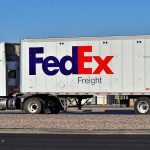
Unleash the power of AI
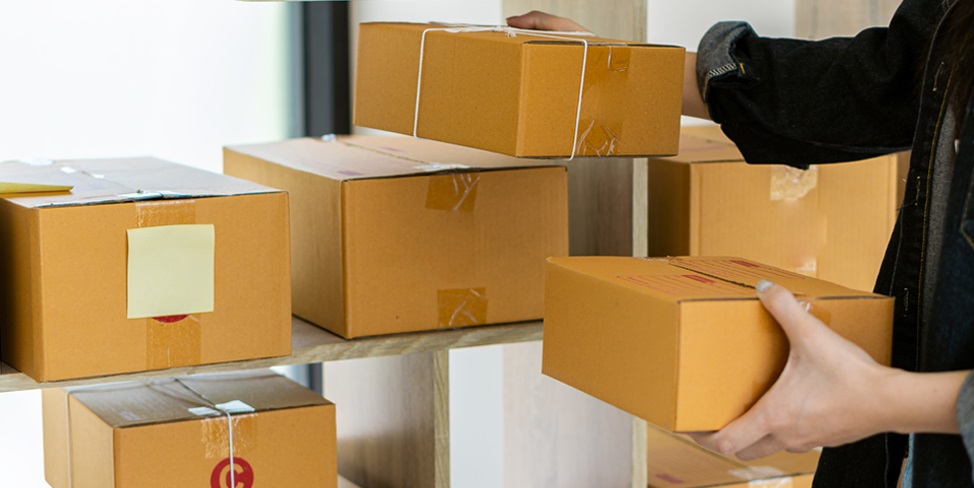
Rising parcel volumes and customer expectations are increasing pressure on every retailer and CEP distribution network. Gathering evidence about the real condition and shape of parcels – and any special labels – has never been more important says Diego Valdivia, Product Manager at Prime Vision.
“What is the real parcel mix? How many parcels suffer damage at a particular hub? How many parcels contain hazardous materials? Getting accurate answers to these questions can help to optimise operations, drive efficiencies and save costs, but the process has thus far been complex to implement on an organisation-wide basis.
Computer Vision specialist Prime Vision has designed a new system that can distribute workloads across a supply chain and gather global information, making artificial intelligence for postal operations more accessible and scalable than ever before.
The application of AI/ML (machine learning) in the parcel sector has, until now, been limited to specific individual operations, processing lines, or hubs. And yet there is vast potential for this technology to bring about genuine change and competitive gain. With this thought in mind, Prime Vision tasked itself with a new way to deliver its full advantages across complete national networks.
Actionable insights
The result of Prime Vision’s development process is the Smart Store, a hybrid system that leverages and complements image intelligence to deliver maximum impact across entire postal operations. The Smart Store goes way beyond answering the operational questions; after data gathering, it aggregates every parcel’s key results in a central control hub to gain a snapshot of the whole network. For any company struggling to maximise the value of ML solutions, the system provides a practical and cost-effective means of converting advanced AI into actionable insights.
Following the aggregation of ML model results, the Smart Store provides a summary in a comprehensive overview that effectively gives operations managers a new tool to compare the performance of sorting centres and key metrics across suppliers. The system converts the results of vision systems into global observations, brings more visibility to entire sorting operations, analyses the sorting mix and obtains evidence-based insights into partner retailers. It is also possible to share sensitive data securely across operations, empowering different departments.
Maximise the use of asset images
Besides becoming the user’s central image archive, the Smart Store utilises existing installed infrastructure to add many state-of-the-art vision systems that make the most of asset images taken in the sorting process.
To explain further, the Smart Store begins by connecting with the customer’s sorting centres. A typical installation uses a local server to connect with the local Smart Integration Management (SIM) platform and extract pictures and metadata from the sorting operation. The customer can then process the data with selected AI models from Prime Vision’s portfolio, like damage detection, parcel mix analysis, and specialized cargo classification. This process is repeated in each sorting centre, allowing the Smart Store to globalize qualitative analysis across the chain.
Prime Vision can then upload the desired processed images and model results to the central Smart Store. From here, the data is aggregated, visualized, and made safely available for distribution and providing the customer with evidence-based insights from across the entire operation.
Measure process quality at scale
The Smart Store allows users to add key analysis tools at each sorting centre with minimum overhead. Simply select any of Prime Vision’s Computer Vision modules, which include: Essentials Suite (lower cloud costs with optimal image selection and encoding); Damage Suite (identify mishandling and troublesome network legs); Real Parcel Mix Suite (determine parcel size and type, and verify that assets are on-spec); Diagnosis Suite (cut camera maintenance costs and understand the reasons behind barcodes rejections); and Specialised Cargo Suite (detect battery labels, hazardous materials, and fragile tags).
In summary, customers can leverage the Smart Store to connect multiple sorting centres and securely archive, share, and aggregate images and metadata. After deploying the Smart Store in their local or cloud infrastructure, users are able to start leveraging the benefits of advanced computer vision on a national scale.”