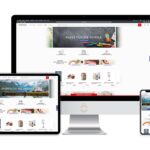
DHLs new hub
Responsible for 100 million shipments a year and with an annual turnover in excess of five billion euros, DHL is a major player in the international express delivery market. The company has recently completed a £35 million investrnent in a new Air Express Hub at East Midlands Airport. One of 35 such hubs around the world, and the biggest in the UK, the new facility is designed for throughputs of up to 24,000 parcels and 18,000 docunients (‘flyers’) every hour.
Given the sheer scale of DHL’s worldwide operation, it is no surprise that the company has developed considerable expertise in effective parcel sortation techniques. For the East Midlands project, a mechanised approach was preferred to full automation. Andy Myatt, global engineering manager for DHL Aviation, outlines the thinking behind this decision: “Our hubs generally have a relatively short operating window – perhaps six hours on a typical night. Of that, peak throughput may extend to no more than two or three hours. It is clearly much harder to justify the additional cost of an automated system when it is only likely to be utilised to its full potential for this length of time. The high growth rates we are experiencing as a business also favours the mechanised approach at East Midlands. Accommodating a rapid rise in throughput would mean that in the early years of its life an automated system would be under-utilised, but within four or five years we would need to extend it.”
Other factors tipping the balance in favour of mechanisation include the absolute standards of robustness and reliability essential in the express overnight delivery business. As Andy Myatt explains: “Obviously it is possible to build redundancy into an automated system, but again this adds to the cost and makes the economic justification harder still.” However, sophisticated bar code track-
ing methods are still employed, ensuring realtime traceability of every parcel and flyer as it passes through the delivery chain.
For a conveyor system capable of meeting a clearly defined specification, DHL turned to Siemens Dematic. Although more commonly associated with automated logistics solutions, the company’s Banbury-based parcel handling system designers proved well placed to meet DHL’s requirements. “The Siemens Dematic team could draw upon USbased sister company Siemens Dematic Corporation’s (formerly known as Rapistan Systems) proven, heavy duty parcel conveyor range to match DHL’s demanding engineering criteria.
Installation of the £5.5 million conveyor system began inJuly 1999 and handover was completed in April 2000. The system basically operates as an interface between DHL aircraft flying in from other international hubs and DHL vehicles arriving from the company’s service centres across the UK. The overall objective is simple: to unload, accurately sort and despatch parcels and flyers as rapidly as possible, ensuring that aircraft and vehicles are ready to return to their original locations in the shortest possible time.
To achieve these objectives, the conveyor system is effectively split into two discrete sortation solutions. one for parcels and the
other for flyers. Typically, incoming aircraft start to arrive at the hub from 9.30pm onwards. Some 80% of DHL flights into the UK now come into East Midlands Airport – a total of 20 aircraft per night. All sorting is carried out ‘air side’ commencing with the offloading process. There are three offload areas for aircraft containers (ULDs) and one for roll cages, which originate from the trucks. Transported from the aircraft to the hub via tugs, each unload area is designed for up to eight ULDs to be unloaded simultaneously. Parcels are placed onto a large slide (flyers onto a high level conveyor), from which point, they undergo a three-stage sortation process that ultimately ensures each individual package is allocated to one of 120 different destinations.
The first (primary) sort consists of DHL staff putting parcels onto one of three, vertically stacked conveyors according to their destination code labels. Parcels are then conveyed up to a secondary sort process on a mezzanine floor. Here a series of semi-automatic diverters ensures an even distribution of parcels across the secondary sortation area, where staff again assign parcels to one of four different conveyors, according to the destination label. From here, parcels are conveyed to the third (tertiary) sort area. where staff perform a ten-way sort to an appropriate ULD or roll cage, ready for onward trans
portation.
On the ‘land-side’ of the hub, vehicles dock at one of 30 loading bays. From this point, parcels are transferred onto the ‘airside’ sortation area and undergo the same sortation process, with the three stage process accurately and efficiently directing packages to the appropriate ULD, ready for loading onto the aircraft.
Flyers from both air-side and land-side are put through a separate three-stage sortation process: three ways in the primary sort, six ways in the secondary sort and up to twenty ways in the tertiary sort. In total, there are some 280 different flyer destinations.
Operating seven days a week, 365 days a year and currently handling 600 tonnes on a typical night, durability and reliability are clearly key requirements of the conveyor system. Siemens Dematic’s experience in this particular field proved invaluable. The company’s standard parcel conveyor is available in widths of up to 1500 mm and offers the capability to handle loads of up to 150 kg/rn. The system supplied by Siemens Dematic is characterised by a number of 90 ( special chutes that reduce the need for powered turns. This minimises both initial and operating costs and also improves reliability and reduces power requirements, as there is one less drive. Siemens Dematic also supplies the conveyor controls and a graphics network that allows the system to be displayed to operating staff on screen.
Judging by the performance of the system to date, DHL’s preference for a manual sortation process is certainly not at the expense of speed or efficiency. Typical wide-body aircraft turnaround time is between 60 and 90 minutes, the type of performance standard needed to stay ahead in such a fiercely competitive market. Furthermore, with a view to the long term, DHL has designed the conveyor system to allow straightforward modular expansion to meet ftiture increases in its international express parcel business.