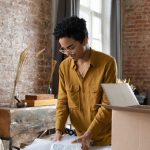
ROI and your YMS
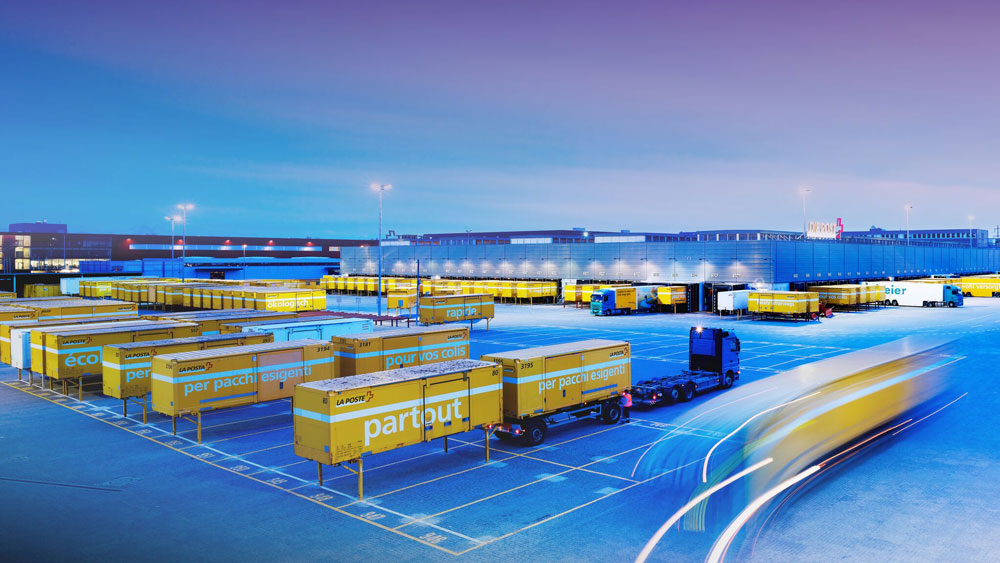
Is your YMS a ‘nice-to-have’ tool or an investment? By Dr. Eva Savelsberg and Matthew Wittemeier from INFORM’s Logistics Division.
Your Yard Management System (YMS) isn’t exciting. In fact, in the scheme of post and parcel operations, it isn’t even a big deal; harsh, but true. You’ve heard the same feature arguments over and over disguised under the vague veil of ‘digitizing your yard’. True, some of these features are ‘nice-to-haves’ but do they add value to your business or simply cost you money to have? While we’ll look at a full range of features later in this paper, let’s start with a quick discussion on ROI. While YMSs are not exciting, a purpose-built post and parcel YMS with optimization built into it can deliver a 100% ROI in as little as 7 months and then drive significant value over its lifespan. How does this compare to a standard YMS? The way the numbers stack up might surprise you.
‘NICE-TO-HAVE’ OR INVESTMENT
A typical YMS might cost you ‘N’, and it might deliver ‘nice-to-have’ features and a little measurable value along the way. But at the end of the year, it still costs you nearly your full purchase cost of ‘N’. Annual ongoing costs will push this out to just over 2x ‘N’ over a ten-year lifespan (see figure 1). There is little added value in a nice-to-have tool.
In comparison, a YMS that delivers measurable value through optimization might cost you 2x ‘N’ but can deliver as much 4x ‘N’ a year in value. After ongoing annual costs are factored in, your post and parcel business stands to earn 36x ‘N’ over a ten-year product lifespan (see figure 1).
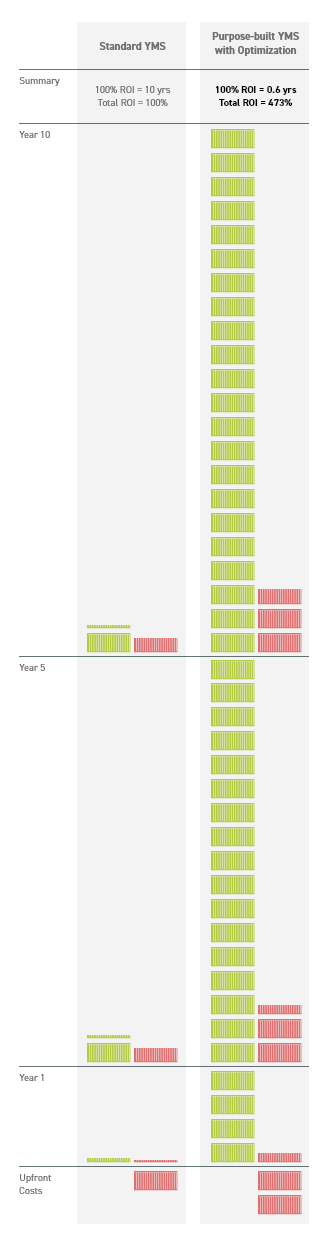
Figure 1 – Cost (red) vs Return (green) for a YMS over a 10 year lifespan.
When you compare the two, the standard YMS will end up costing you more than your initial investment in a purpose-built YMS and you stand to earn minimal value with that tool. In today’s ultra-competitive post and parcel business environment – ‘nice-to-haves’ don’t contribute to the bottom line and things that don’t contribute to the bottom line need to go.
You’ll find YMS software comes in all shapes and sizes – but every system is different and, not all systems have been developed equally. The trick is finding the solution that: best suits your business’s needs today, can grow with your organization for tomorrow, and will deliver the strongest ROI over its lifespan.
Below are our top 11 features post and parcel operators should look for in a Yard Management System. We’ve split the list into three sections – ‘Nice-to-Have’ features, ‘Added Value’ features, and features ‘Specialized’ for parcel operations.
‘NICE-TO-HAVE’ FEATURES
1. Full transparency of the on-site load units and yard resources.
With a YMS, you know where every load unit is at all times because the system logs every incoming and outgoing asset as well as every move they’ll make when they are in your yard. Beyond the time you’ll save every day, you also improve the overall safety of your yard by reducing how many people you have in the yard at any given time which in turn also improves operational efficiency through a decrease in operational disturbances.
Further, a good YMS builds on the full transparency of each on-site asset and provides you with transparency of your yard resources too. Real-time knowledge of the position of each yard truck helps to improve routing and transport decisions as well as yard safety.
2. Faster gate in and out handling.
Through standard, digitized gate processes, the speed of checking trucks in and out of your yard will be dramatically improved. A good YMS will support fully automatic gates as well as manual processing. It should also facilitate communications inside the software when the situation doesn’t match the plan (i.e., the load unit that arrived isn’t what was planned for) so that your site dispatchers can manage the exception inside of their larger plan and communicate that directly to gate staff without the need to switch to email or make a phone call.
3. A calm work environment.
Central to any good YMS is an automated communications platform that allows dispatchers to communicate via the software directly with gate staff and drivers. This removes the need for telephone and radio chatter dramatically improving the work environment for all staff. Automated communications also decreases delays and improves on-time job performance, and improves the accuracy of communications.
4. Data standardization.
Good YMS are designed and configured to support standardized processes. This allows the system to predict good solutions and adhere to constraints within your yard design. They also enable the system to be run in an automatic or partially automatic state when desired. The side effect is that standard processes means standard data. Importantly, this is the crucial first step in setting up advanced analytics for evaluating business KPIs as well as implementing Machine Learning for longer-term process improvement initiatives.
‘ADDED VALUE’ FEATURES
5. Yard vehicle (shunter) optimization.
A high performance YMS comes packed with optimization features, including the ability to optimize your yard vehicle operations. It doesn’t matter if you have two yard trucks or twenty, optimization delivers a range of benefits from reduced travel (fuel savings) through to decreased maintenance and increased asset lifespan (strong asset ROI). When applied to larger yards, with many yard trucks, a good vehicle optimizer can reduce the total number of trucks required to deliver the same service quality level by as much as 34%.
6. Dock door optimization.
Your yard is about feeding your dock doors – and a good YMS will optimize how you manage your dock doors to improve your facilities overall performance. Further, it should be able to automate routine dock door decisions freeing up dispatchers to focus on services that add value to the organization vs. control cost.
A complete knowledge of dock door parameters and status ensures that the YMS adheres to fixed constraints as well as variable ones too. Displays inside the facility that interface to the YMS provide facility staff with real-time information about the load unit at the dock and handheld devices allow them to feed critical information about the unloading/loading process back into the YMS for improved decision-making.
7. On-time performance management.
Advanced YMS systems can receive data from your TMS about load unit contents allowing the YMS to make decisions that improve your facilities on-time performance. As in-bound load units arrive, containers with time critical content are assigned for immediate unloading while standard load units can be stored until a dock becomes available.
8. Priority load performance management.
With data from your TMS, a good YMS will use load unit content data to improve how it handles in-bound load units. Containers containing priority loads will be prioritized over standard priority content. Outbound load units containing priority loads can also be prioritized for discharge from the facility.
9. AI and Machine Learning integration.
AI improves the way users interact with the system (through features like Chatbot) and also enable the system to run autonomously making routine decisions so dispatchers are able to manage more complex exception handling and improve customer service outcomes. Machine Learning enables the system to continuously learn from itself and feed those learning outcomes directly back into the system and/or to human experts for review improving the systems overall efficiency over time.
‘SPECIALIZED’ FEATURES FOR POST AND PARCEL OPERATORS
When evaluating YMS software solutions, the above features can be included in a YMS designed for any industry and any yard environment, but there are also industry specific features which make a select few vendors more suitable for delivering YMS for post and parcel operators.
10. Tight integration with the sortation system.
Through a tight integration with your distribution hubs sortation system, a YMS will be able to improve your sortation systems productivity through improved yard management decisions. At cross docking sortation centers, a YMS with tight integration to your sorter can balance sorting workloads to sub 85%, improve sorter efficiency, minimize shift completion times, and improve safety outcomes in the yard. These outcomes improve the efficiency and handling capacity of your centers most expensive investment, its sorter, through improved yard management decisions.
11. Post and Parcel KPI based performance measures.
Real-time KPIs can transform a business’s productivity but what’s the point of measuring speed if you’re driving in the wrong direction? The best YMS for post and parcel operators provide real-time KPI based performance measures designed for post and parcel operators.
ABOUT INFORM
INFORM specializes in Agile Optimization to improve operational decision making in post and parcel operations.
INFORM’s Agile Yard Management software (YMS), SyncroTESS, optimizes the handling of load units in post and parcel centers. Through the synchronized interaction between gate, yard, and post and parcel center, SyncroTESS enables an efficient, transparent and optimized yard management reducing cost, increasing yard productivity, and improving on time performance. INFORM’s YMS is purpose built for the post and parcel industry with highly specialized features designed to deliver tangible results and measurable value.
More Information:
https://www.inform-software.com/parcel
ABOUT THE AUTHORS
Dr. Eva Savelsberg is Senior Vice President of INFORM’s Logistics Division. She specializes in Agile Optimization Software that renders a wide range of post and parcel processes more productive, agile, and reliable. Eva is also lecturer at the University of Aachen (RWTH), where she received her PhD in mechanical Engineering in 2002. Eva has published 5 books and over 35 papers on innovation in freight transportation.
Matthew Wittemeier is responsible for Marketing and Sales of INFORM’s Logistics Division. He brings over ten years marketing experience from a breadth of industries including aviation, creative, finance, and software services. He holds a Bachelor of Management and Professional Studies from Southern Cross University in Australia.