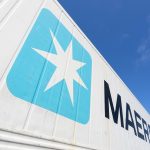
Eighty hauliers, one vision – Pall-Ex's IT challenge
Eighty hauliers, one vision – Pall-Ex's IT challenge
Network operator Pall-Ex decided to write a management system linking its member-companies together without compromising their existing software setup. Peter Rowlands finds out how it was done
Robin Batchford likes a challenge. He must do. Why else would he have taken on the daunting task of writing a brand new Internet-based transport management system from the ground up, and persuading about eighty disparate haulage companies to adopt it?
That was essentially the prospect he faced when he arrived just under two years ago at Pall-Ex, the Nottinghamshire-based national pallet network operator. Yet remarkably, he seems to have pulled it off. The Pall-IT system went live this spring, and by all accounts the implementation went without a hitch.
In IT terms, the problem with pallet networks is the very fact that they are made up from groupings of independent hauliers (see panel on page 34). Inevitably, this means individual member-companies are all likely to have slightly different forms of IT system in place, "and you can't dictate to them what system to adopt," Batchford says. Even major logistics groups often struggle to implement a common IT platform across multiple sites, so the problem for a network of independent companies is clearly that much greater.
However, the Pall-Ex team realised that to compete effectively with the big groups they had to have equally robust and capable systems in place. Hence the appointment of Batchford, an IT professional who had worked in the past for organisations such as the Experian business information group.
What he found was an organisation using the DOS-based Vigo traffic management system, which is popular in the parcels sector. Although this is a mature and capable product, the Pall-Ex implementation meant information flows were often one-way only, and the communication process often relied far too heavily on traditional methods.
"For instance, our central hub didn't know what consignments the members were bringing in each night until they actually arrived," Batchford says. "And discrepancies at the delivery end were only notified by fax when the consignments arrived at the destination depots. Even the hub used fax to notify members of 'hold-overs'." (These are consignments retained for some reason at the hub.)
He therefore spent a couple of months reviewing the whole operation and assessing its requirements. He deliberately avoided studying Vigo itself, and concentrated on building up an ideal-world picture of what was needed.
"It had to be Windows-based, to bring members into the twenty-first century," he says. "It had to introduce a new two-way method of communicating, and to allow members to communicate directly with each other. And it had to be adaptable enough to allow for future expansion."
As an instance of the kind of problem that presented itself, he points to the nature of the collection and delivery task. "Members might either bring collections into the hub or take them directly to a third location. Off-the-shelf software generally didn't allow for that, but we were determined that ours should."
Another priority was to be able to track goods by pallet rather than just by consignment (as most packages do). Average consignment size is just 1.4 pallets, so this requirement was very much in demand among customers.
After reviewing possible off-the-shelf packages, Batchford came to the conclusion that there was nothing really appropriate on the market. So he bit the bullet and set himself the task of writing a bespoke application instead.
What he came up with was a hybrid system that runs locally at each depot (none of your browser-based Java systems here), but which links users with each other and with the hub over the Internet. Programming of the client system was mostly done in Delphi or dBase for Windows, and data is held in local databases. There is also a central hub application, which shares the same look and feel but actually works quite differently, and is built round SQL Server database technology.
Implementation of the system over a dispersed network was always going to be tricky, but Batchford took much of the sting out of the problem by pre-loading the depot-based software on bespoke PCs (one per depot), complete with remote diagnostic capabilities.
The package also includes an Oki dot-matrix printer for producing consignment notes and manifests; these will be replaced by thermal printers, probably later this year, to allow barcode printing as well.
The beauty of the system is that users simply enter job bookings and so on in their existing software, as normal. A new facility is that software allows individual jobs to be marked as Pall-Ex consignments. At a chosen time of day, they give a command to export these jobs to the Pall-IT system, whereupon a list of 40 validation checks is run on them. They are then exported either to the Pall-Ex hub or to another depot.
Clearly for this arrangement to work, the system has to integrate effectively with the user's existing software. However, in practice this was not quite such a challenge as it might appear. Most small and medium-sized hauliers tend to use one of a handful of transport management packages such as Haulmark or Roadrunner, so the main task was to ensure compatibility with these.
Generic interface
Even so, on the face of it this meant writing a bespoke interface with each individual package that members might use. However, the company decided instead to take the high ground and write a generic interface. It then of course had to persuade the other developers to write routines to export their data to it; but Batchford says this was not a problem. "After all, it's extra business for them," he comments.
Hands-on trials were conducted with a Leeds-based member using the Roadrunner package at the turn of the year, and the system worked. Interfaces have now also been developed by Haulmark, Vigo and Zipzap.
Clearly the system stops short of real-time operation, even though Batchford says this was the preferred option. But cost militated against a true real-time system, "and in any case, users can access the system at any time, so in a way we have the best of both worlds."
In choosing the communications system, Batchford wanted something that would be robust, affordable and universal; and at an early stage he opted for the concept of the Internet-based Virtual Private Network or VPN, of which he is a great enthusiast. He likens it to a spider's web. "Every member can access the system for the price of a local phone call, and members can communicate with each other or the hub at will."
Although Internet-based, it doesn't use the World Wide Web, which Batchford considers too slow and unreliable. Instead, it provides secure Internet links to an FTP (File Transport Protocol) server. Six months of trials seem to have proved the soundness of the theory; Batchford says system downtime has been minimal. However, as a backup the company has also created its own Internet Point of Presence (POP) via a leased line to the UUNET facility in Cambridge.
Assured connectivity
"If a member ever has any trouble achieving a connection over the usual Internet system, they simply click a button on the screen, and they are linked directly to our POP instead." This of course commits the member to a national-rate phone call instead of the usual local-rate call, but members have to accept this in the service-level agreement they sign. "In practice it only happens rarely, and it's a small price to pay for assured connectivity."
The current implementation of the Pall-IT system is only the first phase. The system already allows proof-of-delivery handling by reconciling despatch and booking-in details; now barcode scanning and tracking of consignments are under development, opening the possibility of near-real time PODs. Scanning will be introduced at the hub first, probably in the autumn, then at depots.
"It would be great to go the last mile and issue all drivers with handheld terminals," Batchford says ruefully. "Then we could offer true real-time scanning. But in a system made up of individual companies with their own priorities, that's not really viable at the moment."
Meanwhile, though, Batchford has been converting an existing customer "implant" system based on the Vigo suite to work on the new system. The new system is essentially a cut-down version of the depot software, allowing major-account customers to print their own labels and documentation. There are about 20 "hub account" customers of this kind, and most use the existing system.
There are also interfaces with other software to build. This might include further traffic management systems if the need arises, plus accounting systems such as Sage.
A further development could see the system being implemented on the Continent. Pall-Ex plans to apply its existing network model in various near-European countries, probably starting with France and Germany, where it would look for national licensees. Batchford says Pall-IT has been written with such expansion in mind. "It uses a generic gazetteer, and doesn't require leased phone lines. Users can access it through any Internet Service Provider for the cost of a local phone call."
Having done much of the initial coding himself, Batchford is now able to stand back from that task. The in-house team now includes two other software developers and two support staff. "So we can run two or three implementation projects concurrently."
As the implementation date loomed, teams from the member-companies were brought to the central hub in groups of seven for a day's induction training.
The moment of truth for the system came when it went live on a network-wide basis. "You couldn't implement it piecemeal," Batchford says. "Everyone had to go live from day one." It's a measure of the success that implementation was just four days late. That's an achievement the team will be looking to equal as the roll-out goes on. Multiple resources – one objective
The emergence of the pallet networks was a phenomenon of the nineties, and is one that has now spilled over into the new century. Traditionally, consignments of less than a truckload but more than a parcel have always been difficult for the transport industry to handle economically. Pallet networks were conceived as a solution to this problem.
The concept is elegantly simple. Locally-based haulage companies trunk pallet-loads destined for other parts of the country into a central hub, usually overnight. The pallets are then sorted by delivery area and taken back to base by the hauliers serving each area, ready for delivery next day. Participating companies retain their identity and independence, but gain from the economies of scale and access to a national distribution network. The network operator provides the hub and charges a handling fee.
At least half a dozen competing networks have emerged in recent years, and more always seem to be in the making. They vary in structure; sometimes (as with Pall-Ex) the hub is owned by a separate company, while at other times it may be run by a member-controlled consortium.
By common acknowledgement, a "big three" have emerged (Palletline, Palletways and Pall-Ex), and Pall-Ex claims to be in the top two. It was set up by former TNT executive Hilary Sharples in 1996.